Who does Chick-fil-A choose to install their walk-in’s? RSI of course!
Who does a fast food provider call when they need to update their restaurant walk-in cooler and walk‑in freezer? Refrigerated Specialist, Inc. The same people you can call for your needs.
Chick-fil-A is a major player in the fast food business. When they place a restaurant in a market, it quickly becomes one of the major players in that space. After a few years of heavy use, Chick-fil-A will sometimes revamp a restaurant or expand it based on the revenue and market-share generated.
In Waxahachie, Texas earlier this year, Chick-fil-A closed its store for a four week makeover.
They added 700 square feet of new space and completely revamped the kitchen and front of house areas. This included a double drive-thru line and ripping out all the old equipment and installing all new equipment.
After 10 years of use, a walk-in cooler and a walk-in freezer are ready for an update.
RSI was able to schedule the installation of both a walk-in freezer and walk-in cooler to correspond to the tight timeframe and deadline requested by Chick-fil-A.
The design studied, the parts ordered, and delivery scheduled.
The parts arrived from the manufacturer exactly as requested by RSI. The RSI installation team arrived on time to unload and check the order. Once the order was verified, RSI signed off on the delivery.
We will only cover the walk-in freezer assembly and installation here. For more on the installation of a walk in cooler, check here.
Walk-In Freezer Assembly Staging
The installation team staged the assembly of the walk-in freezer and walk-in cooler in the parking lot to remain out of the way of the rest of the trades in the building working.
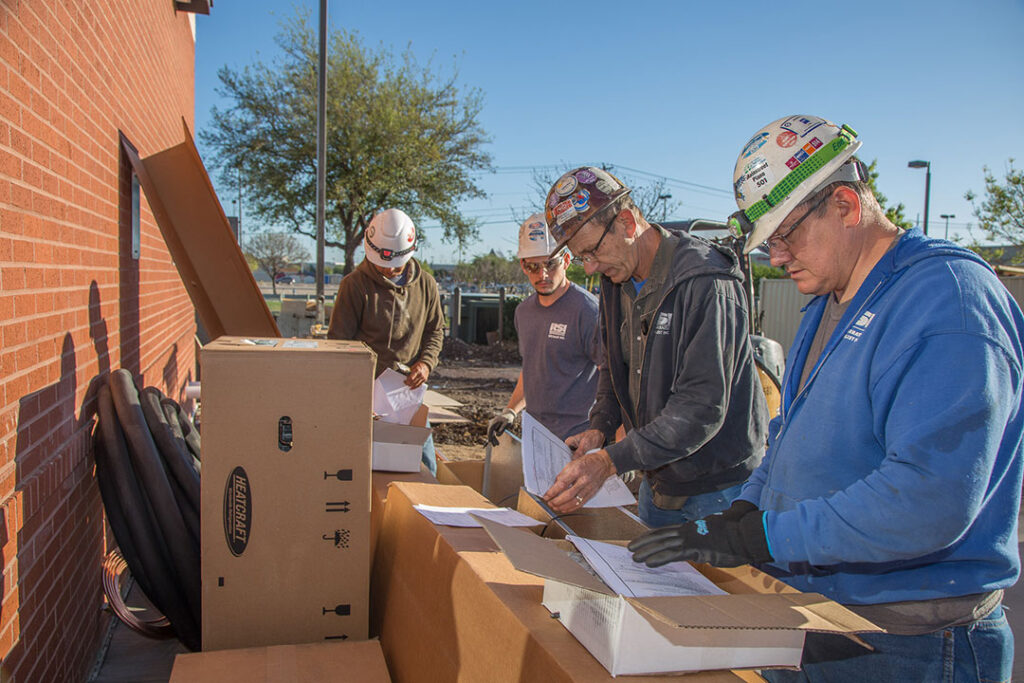
Floor Assembly
Assembly of the walk-in freezer was first.
The installation team set the floor in place after verifying the space was clean and the right size.
A small gap must be available around the complete unit to help with reducing thermal bridging; the process of an adjacent surface transferring heat to the walk-in-freezer.
Once RSI installed and aligned the floor assembly, the wall assembly was next.
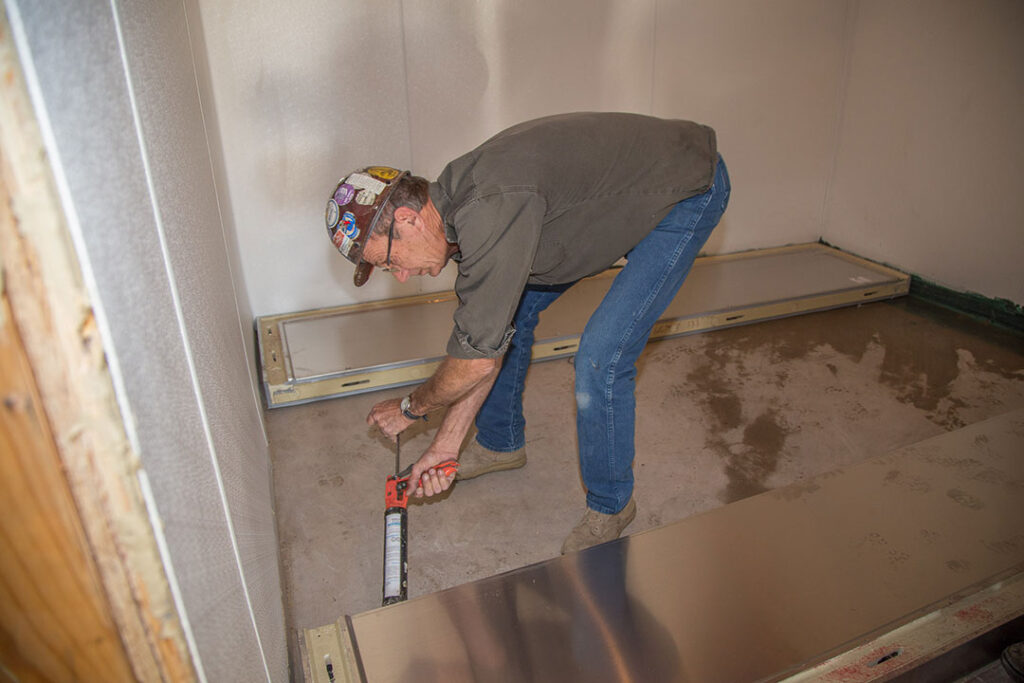
Wall Assembly
The wall construction is the process of bolting individual panels together in the right order to create an enclosure. This process starts in a corner opposite of the door and works around to the door.
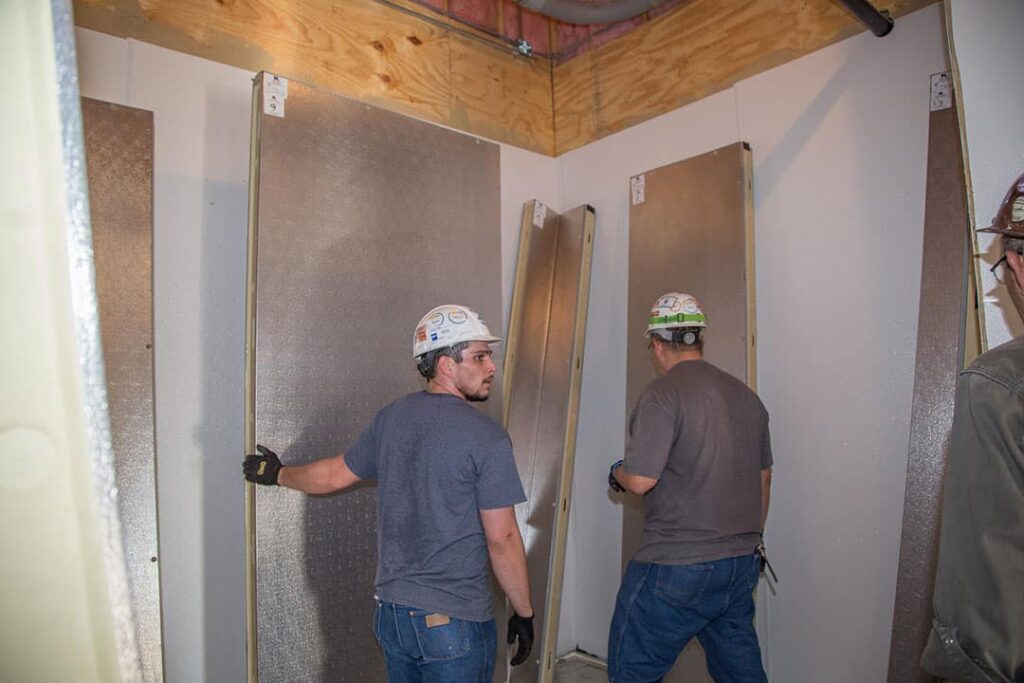
Door Assembly
The door is the last item assembled in the wall section. The weight of the door requires it to be dollied‑in, before assembly. Once the door is in the upright position, it takes a few people to place it into position before being secured. The correct assembly will provide trouble free use while in operation.
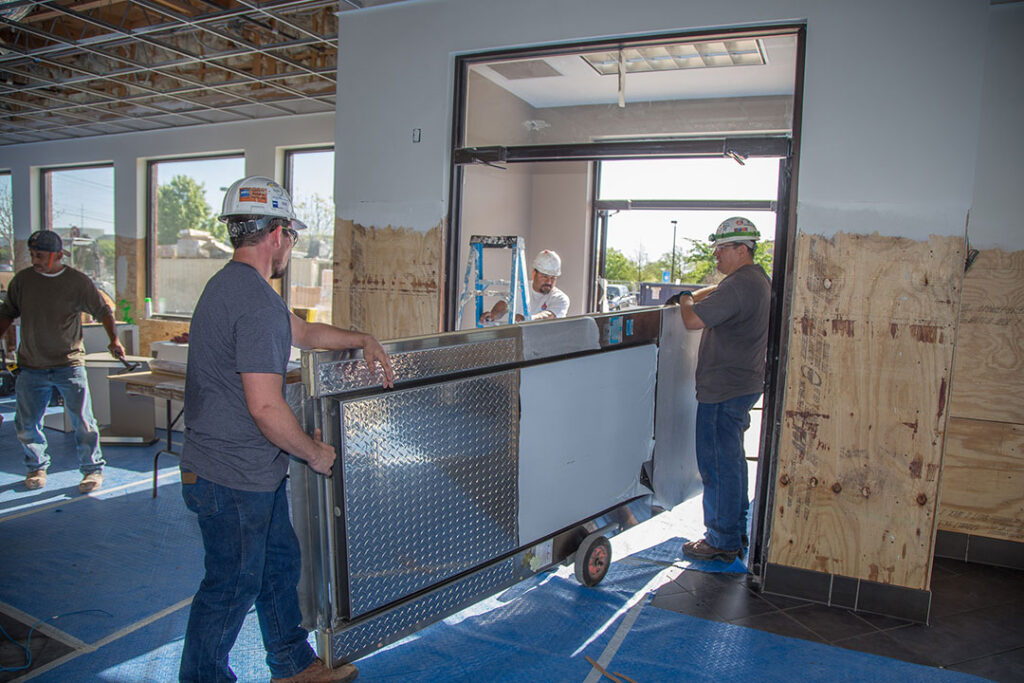

Roof Assembly
The roof of a walk-in freezer is assembled along with the walls. This allows some ceiling panels to be placed on top of existing roof panels before assembly. It is easier to get the ceiling panels in place before all the walls are fully assembled.
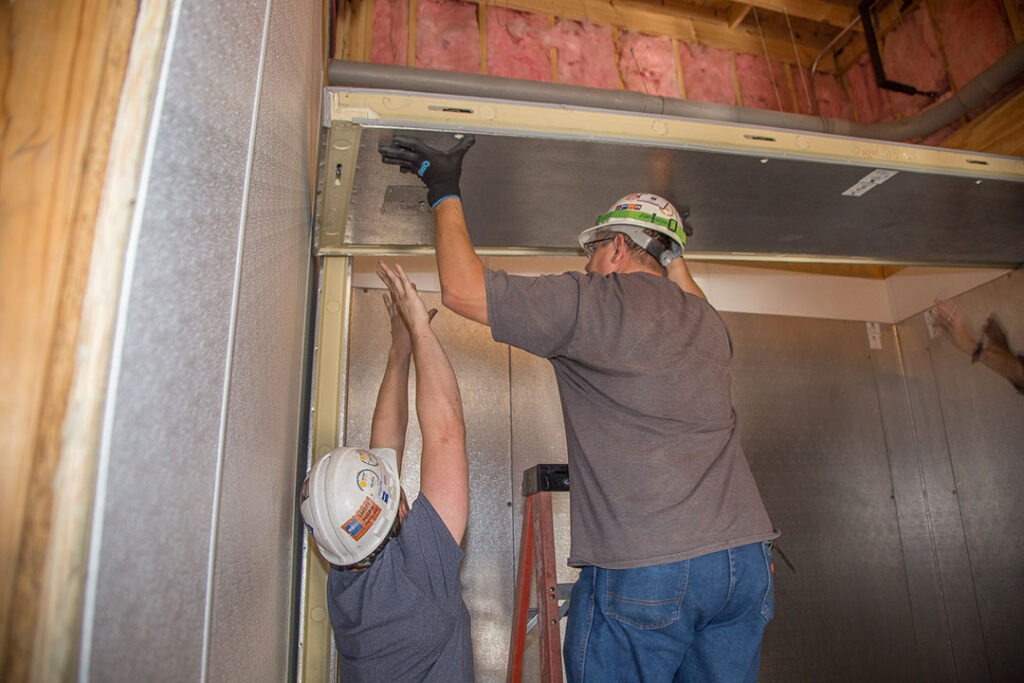
Walk-In Freezer Condenser Installation
Once the floor, walls, and ceiling are assembled, the condenser is next to be installed. The RSI assembly team places the condenser in the correct location and marks the mounting holes. Once the holes are drilled, rods are pushed through from the top of the roof. The condenser is then bolted to the rods, and supported by the roof assembly.
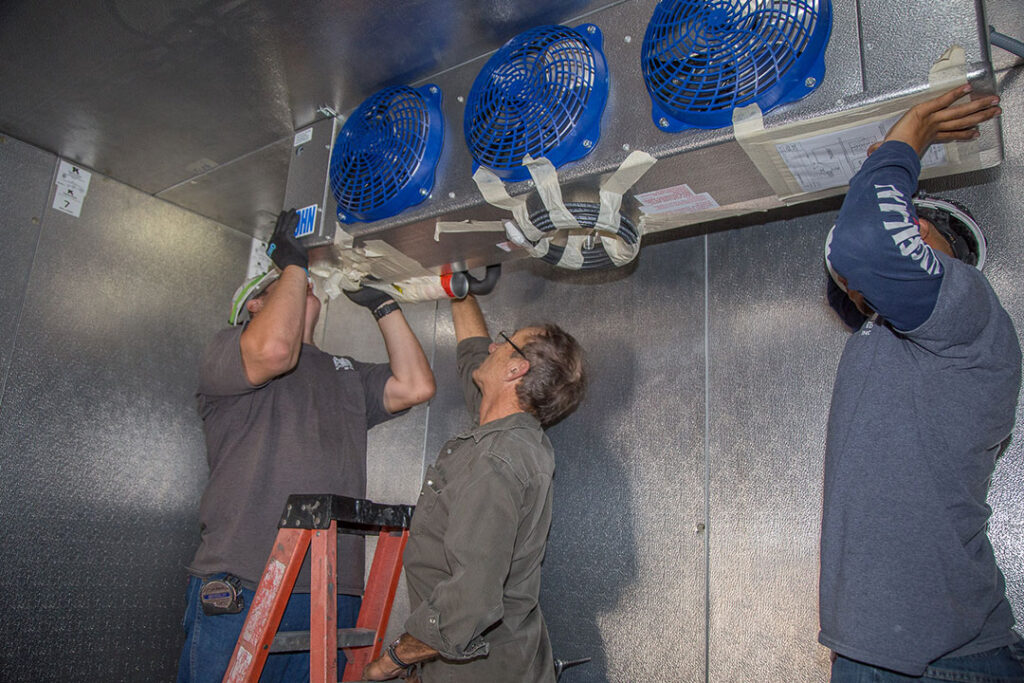
A Successful Walk-In Freezer Installation
Sounds simple enough until you try it. Not all floors are level. Not all walls square, true, or plumb. Therefore, having a dedicated and experienced assembly team is key to installing your walk-in cooler or walk-in freezer.
A team with the knowledge to know what is critical, and what is not, is vital to a smooth and successful installation and assembly of your walk-in freezer. That’s why Chick-fil-A chose RSI and why you should too.
Contact RSI for all your commercial refrigeration installation needs.
Phone: 972-279-3800
Toll-Free: 888-TOO-WARM
Service Email: RSIService@rsidfw.com